2024 CONFERENCE SCHEDULE

Two Conference Tracks
TRACK 1: On-Site Utility Sustainability: Energy & Cooling Water Conservation
Receive actionable project ideas on how to reduce the water and energy consumption of your plant. Learn the latest system assessment techniques from world-class auditors. Learn technology deployment strategies from leaders of associations like the Compressed Air & Gas Institute. Meet experts who can answer questions regarding system automation, measurement and monitoring to verify energy savings. Receive 8 PDH credits.
TRACK 2: On-Site Utility Reliability, Safety and Quality
Learn techniques to improve production up-time with high-quality and reliable on-site utilities. Discuss the establishment of compressed air specifications and compliance verification for the safe production of food, beverage and drug products – and to reduce production spoilage/reject rates. Receive maintenance check-lists and training to maintain required pressures and flows. Learn technology deployment strategies from leaders of associations like the Cooling Technology Institute. Receive 8 PDH credits.
TRACK 1: On-Site Utility Sustainability: Energy & Cooling Water Conservation
Tuesday, October 29th – 8:00 – 10:00 AM
Session #1: CAGI Education Seminar – Case Studies in Maximizing Compressed Air Efficiency
Chair: Chad Larrabee, Vice President, Tendering, Project and Product Management, Ingersoll Rand – NA Compression Systems and Services
Through real-world case studies and practical examples, CAGI’s educational seminar will illustrate the measurable energy savings, environmental and safety benefits that can be achieved. From system design and component selection to maintenance strategies and energy audits, attendees will gain actional insights to enhance energy efficiency and safety in their own facilities.
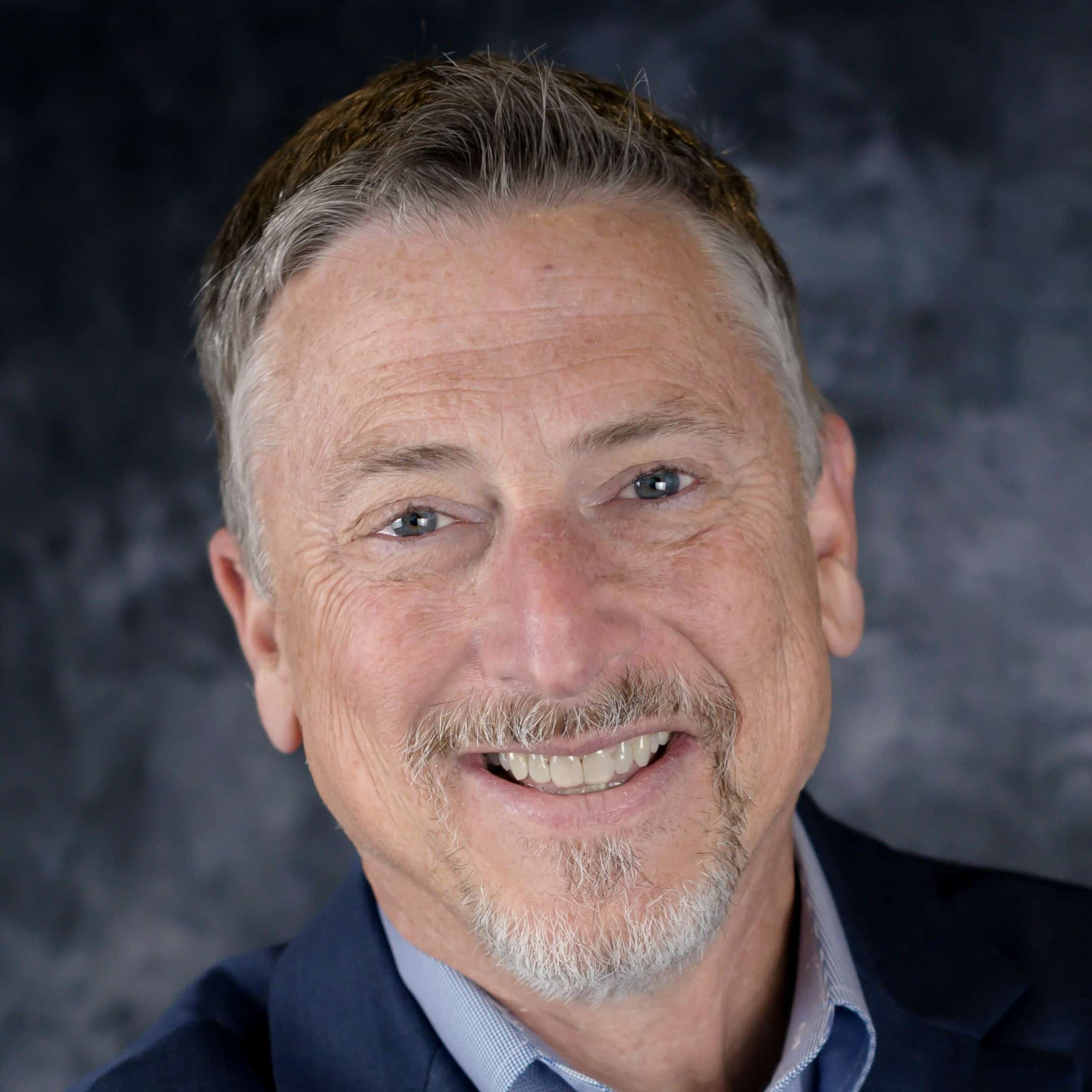
Speaker #1: Redesigning Greenfield Site Systems to Meet True Demand
Neil Mehltretter, Technical Director, Kaeser Compressors
Each year thousands if not tens of thousands of compressors and compressed air stations are designed and built per a specification. Many of those new installations are completed for Greenfield or new construction. In these cases, specifications for flow, pressure and air quality can vary widely from the eventual true demands. The two case studies discussed will follow two such Greenfield projects where the demands were much lower than expected. We’ll review how this was evident at the plant level, and what solutions were considered to address what the industry refers to as “oversizing.”
As Technical Director, Neil Mehltretter oversees Kaeser’s Technical Department with responsibilities including product management and system design. An authority on compressed air assessments, Mehltretter has conducted and supervised thousands of industrial compressed air studies, helping users achieve significant energy savings and operational improvements. He has a bachelor’s degree in chemical engineering from The University of Florida and holds several industry certifications.
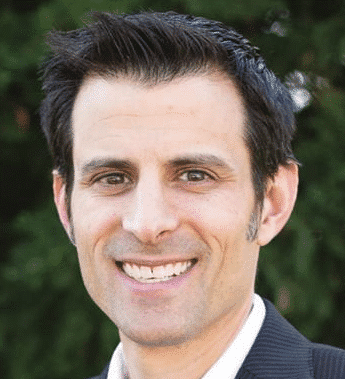
Speaker #2: Improving Energy Efficiency in Systems with Multiple Centrifugal Air Compressors
Mark Krisa, Strategic Account Manager, Ingersoll Rand
This presentation will cover the analysis and corrective actions implemented for two compressed air systems consisting of multiple centrifugal compressors. Both case studies will explain the original state of the system and post implementation results using collected data. Content will include charts and other graphics to summarize operational changes and quantified results.
Mark Krisa is Strategic Account Manager at Ingersoll Rand. A graduate with a degree in engineering science from the University of Western Ontario in Canada, Mark has worked in the compressed air industry for over 30 years. His experience in the industry is diverse ranging from compressor service technician through engineering, compressed air system auditor and product management. Mark has authored several papers and is a project member with CAGI, ISO and CSA.
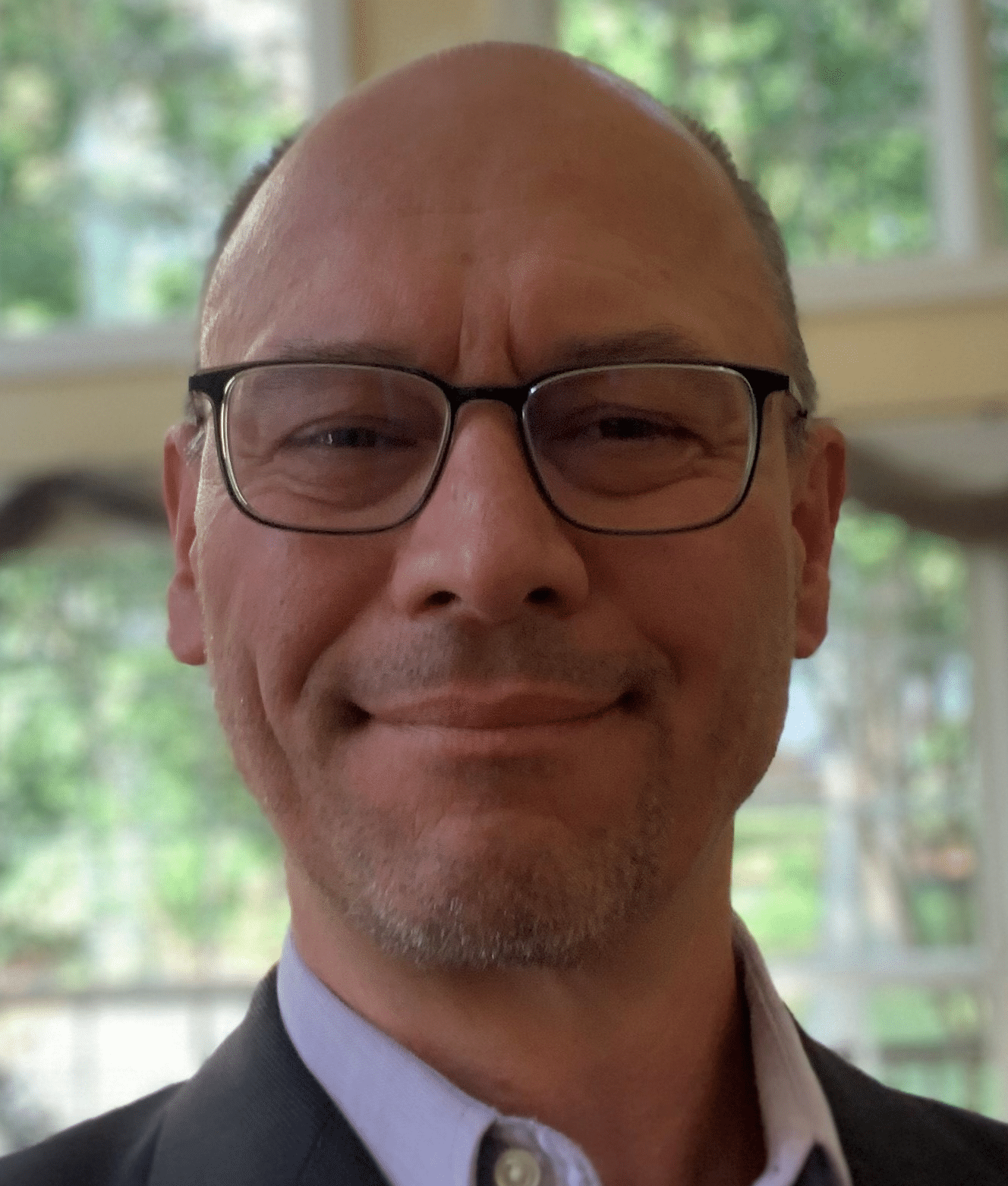
Speaker #3: Multi-Plant Campus Supply & Demand System Optimizations
Frank Moskowitz, AIRScan Expert, Atlas Copco Compressors
Case Study #1: A multi-building manufacturing campus, with two separate but interconnected compressor rooms, was experiencing insufficient pressures, air leakage, control gaps and other issues. This presentation will cover the solutions that were implemented to stabilize operating pressure, improve reliability and reduce the systems’ carbon footprint following a system assessment.
Case Study #2: An aging compressed air system was not responding to demand and experiencing reliability and maintenance issues. In order to improve reliability and consolidate multiple compressed air applications throughout the campus, an assessment was performed to identify ideal solutions. This presentation will provide the implemented solutions, and the positive results.
Moskowitz has an extensive background with over 45 years’ experience in plant engineering. He has a degree in mechanical engineering and education, including the refrigeration, electrical, and plumbing trades. His specialty consists of Compressed Air Systems (oil-flooded and oil-free), vacuum systems, contaminate removal, system design and energy management. Moskowitz is a Compressed Air Challenge instructor for the Fundamentals and Advanced level of training, and an AIRMaster+ instructor. He is also Vice-Chair for ASME Standard EA-4-2010 “Energy Assessment for Compressed Air Systems”; and is a member of the ISO technical committee for Air Compressors and compressed air systems energy management; TC118/SC6/WG4.
Speaker #4: Blower Technologies: Reducing Noise Emissions in a Bulk Process Facility and Optimizing Efficiency in a Wastewater Plant
Jason Costigan, Director of Product Management, Gardner Denver
Case Study #1 Bringing Down the Volume: Large bulk process facilities require a great number of blowers to move material throughout their numerous pneumatic conveying systems. In this case study, a facility was using over 90 positive displacement blowers to move milled limestone throughout the plant which can mean high levels of noise generated from the blowers. For plant employees, a quieter solution meant a safer and more comfortable work environment. This presentation will cover the design solutions that were implemented to reduce noise levels to make a more comfortable work environment for employees.
Case Study #2 Turndown and Long-Term Energy Consumption: Blower efficiency is a top priority during the design of a wastewater treatment plant, specifically its aeration equipment. Aeration generally accounts for 50 to 60% of the energy consumption at a treatment plant. Optimizing the efficiency of blower performance by accommodating inevitable changes in flow is essential for controlling energy costs. This presentation will include the different types of blower technology required for efficient turndown in wastewater applications.
Costigan is Director of Product Management at Gardner Denver. He graduated with an MBA from Quincy University in Quincy, IL. Costigan has worked in the blower industry for over 15 years. His experience in the industry is diverse ranging from focus on transport blowers, industrial blowers, and blowers used in the wastewater industry. Costigan is currently serving as Vice-Chair of the blower and vacuum section of CAGI.
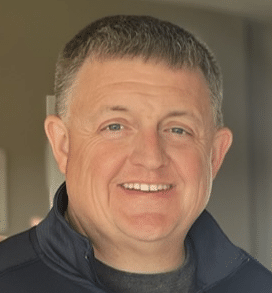
Wednesday, October 30th – 8:00 – 10:00 AM
Session #2: Expert Panel Discussion
How to Design Compressed Air Systems Compliant with the ASHRAE 90.1 Commercial Building Energy Code
Panel Moderator: Paul L. Baker, PE, Senior Mechanical Engineer, Jacobs
- Section 1 – Air Compressor Part-Load Control and Efficiency, Options 1 & 2: Neil Mehltretter, Technical Director, Kaeser Compressors
- Section 2 – Energy-Saving Controls for Systems with 3+ Air Compressors (total input power ≥150 hp): Tim Dugan, PE, President, Compression Engineering Corporation
- Section 3 – Compressed Air Energy and Demand Monitoring System-KPIs to Measure and Data Log (total input power ≥150 hp): Martin Zeller, Country Manager, CS Instruments USA, Inc.
- Sections 4 & 5 – Compressed Air Piping System Leak Testing and Sizing Specifications: Panel Member TBD.
Paul L. Baker, PE, LEED AP BD+C, CPD, GPD
Panel Discussion Reference Article: ASHRAE 90.1 Brings New Requirements to Compressed Air System Design.
TRACK 2: On-Site Utility Reliability, Safety and Quality
Tuesday, October 29th – 8:00 – 10:00 AM
Session #1: CTI Seminar – Cooling Towers in Industrial Plants
Session Chair: Frank Foster, CTI Membership Committee Chair
Speaker #1: Sustainability and Reliability for Towers
Mark Pfeifer, PE, Sr. Manager, Technical Services, SPX Cooling Tech
Mark Pfeifer, PE, LEED AP BD+C, Overland Park, KS, SPX Cooling Tech: Mark holds a BSME in Mechanical Engineering from Kansas State University, is a registered Professional Engineer in the State of Kansas and is a LEED accredited professional. His cooling tower career spans over 30 years in various roles including materials engineering, proposal management and applications engineering. In his recent role Mark manages the Technical Services department providing technical support for sales representatives and customers. Mark is currently secretary of ASHRAE’s Technical Committee for Cooling Towers and Evaporative Condensers (TC8.6) and a member of USGBC. Mr. Pfeifer has done numerous presentations to engineers, architects and contractors on the subject of cooling towers and their application to HVAC and Industrial projects.

Speaker #2: Rx: Re-Energizing Your Cooling Tower with Performance, Quality & Savings
Bill Miller, PE, Managing Partner, L S Enterprise
Cooling towers lose efficiency over years due to multiple factors such as the buildup of scale and/or fouling and the deterioration of various components due to age, wear, and tear. Loss of cooling efficiency drives up energy costs when the cooling tower fan runs more often at full power trying to meet the set point and when downstream equipment, such as a chiller, receives inlet water that is warmer than design. Wet cooling towers benefit from the thermodynamic advantages of evaporative cooling vs (dry) air cooling, but degraded drift eliminators and inlet louvers can waste water if it escapes from the tower. When it comes time to replace components, tower owners have choices and options to satisfy their requirements of performance, quality, and cost savings. The presentation focuses on fills, drift eliminators, and louver products used in modern tower repairs when discussing these factors.
Bill Miller is a Managing Partner of L S Enterprise LLC and is a licensed Professional Engineer in the Commonwealth of Pennsylvania. Bill has been in the cooling tower industry for over 25 years, having worked at Brentwood Industries for over 20 years, ending as their Director of Application Engineering in charge of all global cooling tower technical concerns and all corporate R&D functions. Bill has a Bachelor of Science in Aerospace Engineering from the Pennsylvania State University, is a member of Tau Beta Pi, the National Engineering Honor Society, and has presented multiple papers at Cooling Technology Institute (CTI) and Electric Power Research Institute (EPRI) conferences. He is currently Vice-Chair of CTI’s R&D Committee.
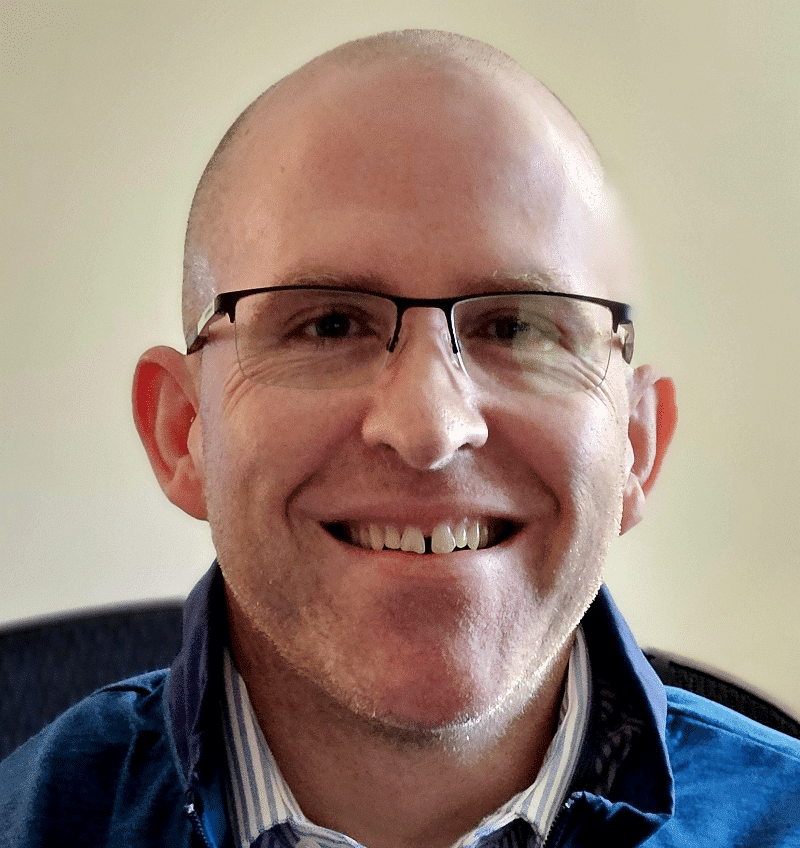
Speaker #3: Cooling Tower Water Reuse
Jon Cohen, Digital Innovation Fellow for Buckman Chemical
Jon Cohen will cover treated municipal wastewater as a viable makeup water source for a cooling tower.
Jon has been involved in water treatment for over 30 years, covering laboratory, R&D, sales, equipment, technical consulting, and management. He has been the Technical Director for regional water treatment companies and led large teams in biocides and equipment for a larger company. He is an active participant in trade organizations, serving as a past BOD member at the CTI and participating in the drafting and subsequent adoption of numerous standards and guidelines, including ASHRAE/ANSI 188. Jon holds a bachelor’s degree in biology, master’s in chemical engineering, and an MBA. He is also accredited with LEED AP. Jon is currently a Digital Innovation Fellow at Buckman Chemical. Jon lives in Naperville, IL with his wife, daughter and three dogs. He loves to travel with his family and play golf and tennis. Jon is also active in Leadership and mentoring programs through Sigma Chi and Northern Illinois University.
Speaker #4: Save Time and Money with Closed Loop Cooling Solutions
Jason Heilbrunn, Applications Lead – Industrial, Baltimore Aircoil Company
Learn how clean, closed loop heat rejection systems can benefit your facility. Several alternatives to close the loop will be explored, including open cooling tower & heat exchanger combinations, closed-circuit cooling towers, and dry and adiabatic designs.
Jason holds a BS in mechanical engineering from Syracuse University and an MBA in finance from Loyola University of Maryland. He began his career as a Mechanical Design Engineer for a major engineering consulting corporation before accepting a position with BAC. Jason has held various roles within BAC including Aftermarket Engineer and Sales & Applications Engineer. In his current role as the Industrial Applications Lead, he manages the Industrial Applications group to ensure that all light and heavy industrial customers receive the highest level of technical support. Jason has given numerous presentations to engineers and end users for a variety of applications in the HVAC and Industrial spaces.
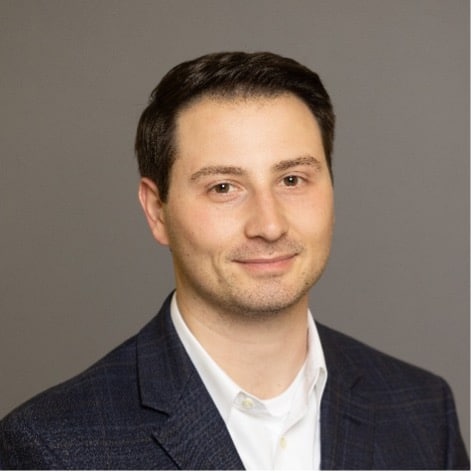